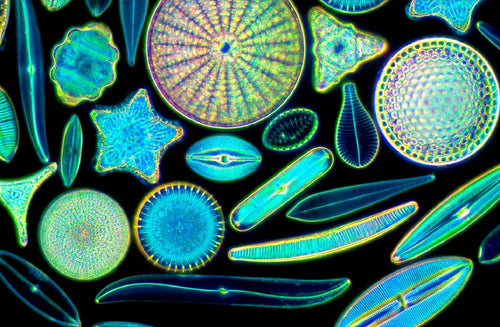
Diatoms - Nature’s Jewels viewed with a Microscope
Motic America
Diatoms are unicellular algae (Division Chrysophyta, Class Bacillariophyceae). Diatoms are microscopic in size, live in water, soil and moist en...
Read ArticleDiatoms are unicellular algae (Division Chrysophyta, Class Bacillariophyceae). Diatoms are microscopic in size, live in water, soil and moist en...
Read ArticlePosted by Motic America on
Printed Circuit Boards (PCBs), also known as Printed Wiring Boards, can be extremely complex components with multiple circuit layers. Manufacturers of these products must sample the production for quality control and assurance, the methods of which we will go over in this article.
There are many approaches and techniques to test production quality. There are 3 classes of PCBs, and based on the class the PCBs may require testing with varying degrees of critical tolerance. For example, Class 1 would be part of non-critical, replaceable limited life products such as garage door openers. On the other hand, Class 3 PCBs would include uses where high performance and reliability are critical. Most Class 3 PCBs would see use in aerospace, military systems and medical devices.
In critical products, Cross-section Analysis (microsectioning) is not only highly useful in QC/QA but also in Failure Analysis. Cross-sectioning is the process of cutting the PCB in the desired location of interest to produce an approximately one-inch square piece of the PCB. This piece is placed into soft acrylic that hardens around it, where it is then fit onto a metallographic mount which is in the shape of a hockey puck. This mount is then polished to produce a smooth surface of the PCB cross-section for microscope viewing. The mount may also be etched to produce improved viewing of copper grain structure, and also to make the copper layers more visible.
A good way to perform destructive cross-section analysis is to fabricate a few extra boards called PCB Test Coupons, which can be used to evaluate the performance of the board’s production. Test Coupons are designed to have the same specifications as the end product PCB. They are tested to identify manufacturing and material defects.
During the PCB fabrication process multiple PCBs are fabricated on one large board called a panel. The PCB Test Coupons are usually not a part of the core PCB panel, and are typically created around the edges of the large panel. These coupons are then cut from the panel and the area of interest can be cut vertically or horizontally, depending on what structures need to be examined visually.
This cross-sectioning process exposes many points of interest for measurement and inspection such as plating thickness, thickness of dielectric laminate material, evidence of cracking, etc. Many of these types of measurement and inspection points will be discussed below. The criteria for inspection are often specified by the customers (for example, with IPC 6012, a performance specification document). Additionally, the coupon design follows standards like IPC’s 2220.
Inspection and measurements are accomplished using a reflected light microscope (metallographic microscope) with digital camera and software to measure and document the various points of interest. As mentioned previously, the PCB section is in acrylic material in the shape of a hockey puck. With this in mind there are two types of microscopes to choose from each with their advantages and disadvantages. It is up to the user to select which is best for their use.
The first type of microscope is a usual “upright” microscope which has the lens looking down on the surface of the sample. The advantage is the you can see you sample surface and place it under the lens as needed. The disadvantage is that the hockey puck may not have parallel top and bottom surfaces, which may make the sample unlevel and require constant refocusing. Even worse, certain regions of interest may not be in focus from one side to the other in the field of view. This can be overcome by using a metal plate on the microscope sample stage, and placing modeling clay between plate and bottom surface of the puck. By using a leveling press to make the surface parallel, the polished surface can be brought to a level height.
However, despite the flexibility of an upright scope, the above method takes time for each sample. The alternative is to use an “inverted” microscope which has it lens pointing upward. This has the advantage where users place “hockey puck” samples face down on the stage, and therefore do not require leveling. The disadvantage is that users can no longer see the sample position visually and may require hunting for the area of interest, or switching to very low magnifications to get a larger area of view. The final choice is ultimately up to the user and their form of material applications.
In our other article, we detail the types of measurements and defects that users can go through using upright and inverted microscopes.
Related Products
Models | ||
Features |
PA53 MET provides customizable optics and lighting systems, such as BF, BF/DF or DIC. This microscope can be upgraded to a motorized stage for Low Magnification Tiling of large samples. |
The PX43MET is an inverted materials microscope that features BF, DF, and Polarization. But unlike most inverted microscopes, it also features DIC, which adds incredible depth and elevated features to your imaging. |
Want to know which microscopes fit you best? Fill in the form below and our specialists are glad to help!